Telecommunication towers are considered the backbone of telecommunication systems. These towers provide important aspects in transmitting the signals or radio coverage. As the telecommunication towers age, maintenance for each site is increasingly important. Often, telecommunication site equipment is used without a planned maintenance approach. Such a strategy results in unplanned downtime which often leads to unexpected critical failures. Scheduled maintenance replaces components frequently to avoid unexpected equipment stoppages, but increases the time associated with sites’ non-operation and maintenance costs. Moreover, the emergence of Industry 4.0 has led to the wide use of sensors that have facilitated telecommunication operations and increasing attention to maintenance strategies that can decrease the cost of downtime and increase the availability of telecommunication towers.
There are several definitions of maintenance in the literature. Mohamed Sallak, Ph.D. and Associate Professor/HRD at the University of Technology of Compiègne, and ITD Research partner shares his scientific insight through a new series of articles dedicated to maintenance.
©Photo: Pastel France
Overview of all maintenance types
The most well-known definition of maintenance is described by the norm EN 13306: maintenance is “the combination of all technical, administrative and managerial actions of an item intended to retain it, or restore it to a state in which it can perform its required function“. We distinguish different types of maintenance: corrective maintenance, preventive maintenance, and predictive maintenance (cf. Figures 1 and 2). The norm EN 13306 also provides a classification of maintenance types.
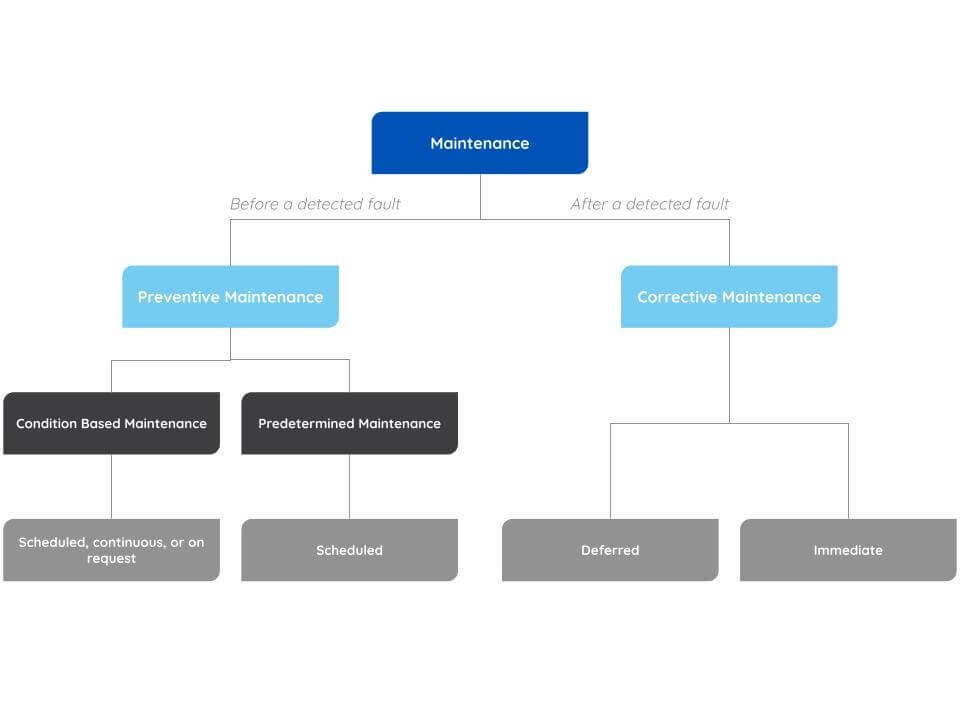
Figure 1 – Overview of all maintenance types [EN13306]
Standard terminology
The oldest form of maintenance is corrective maintenance, also called reactive maintenance. Corrective maintenance is “carried out after fault recognition and intended to restore an item into a state in which it can perform its required function”.
Preventive maintenance is another form of maintenance that is “carried out in accordance with established intervals of time or number of units of use but without previous condition investigation. Interval of times or number of units of use may be established from knowledge of the failure mechanism of the item”.
Predictive maintenance is defined by the norm EN13306 as “a condition-based maintenance carried out following a forecast derived from the analysis and evaluation of the significant parameters of the degradation of the item”.
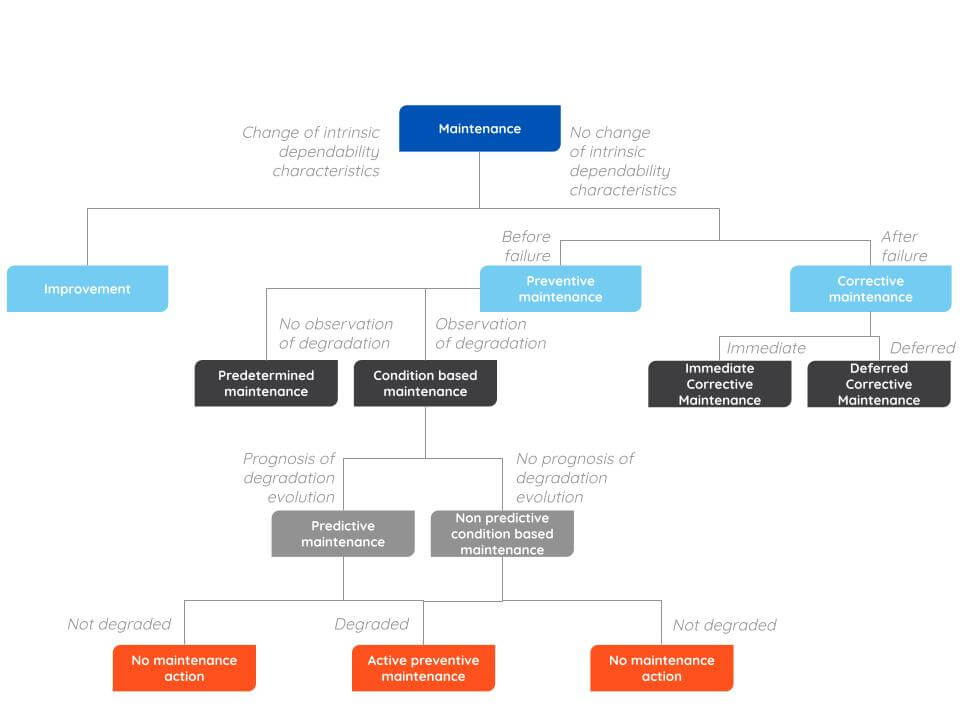
Figure 2 – Detailed view of all maintenance types [EN13306]
Predictive maintenance vs preventive maintenance
Predictive maintenance is a work that is scheduled in the future based on the analysis of sensor measurements and formulas.
Condition-based maintenance is work that is performed at the exact moment in which measured parameters reach unacceptable levels.
Preventive maintenance involves inspecting and performing maintenance on machinery, regardless of whether or not the equipment was in need of maintenance. This maintenance schedule is based on either a usage or time trigger. For example, a tower unit is serviced every year before winter. Also, preventive maintenance does not demand the condition monitoring component that predictive maintenance does. By not requiring condition monitoring, a preventive maintenance program does not involve as much capital investment in technology and training. Lastly, many preventive maintenance programs need manual data-gathering and analysis. While preventive maintenance is determined by using the average life cycle of an asset, predictive maintenance is identified based on preset and predetermined conditions of specific pieces of equipment, utilizing different technologies.
Steps of principal maintenance strategies
The outcome of the different strategies is a reasoned case for why each of the options of predictive, preventive, or corrective maintenance should be carried out on the site equipment, and whether a combination of types is appropriate. Figure 3 gives an overview of the steps of principal maintenance strategies:
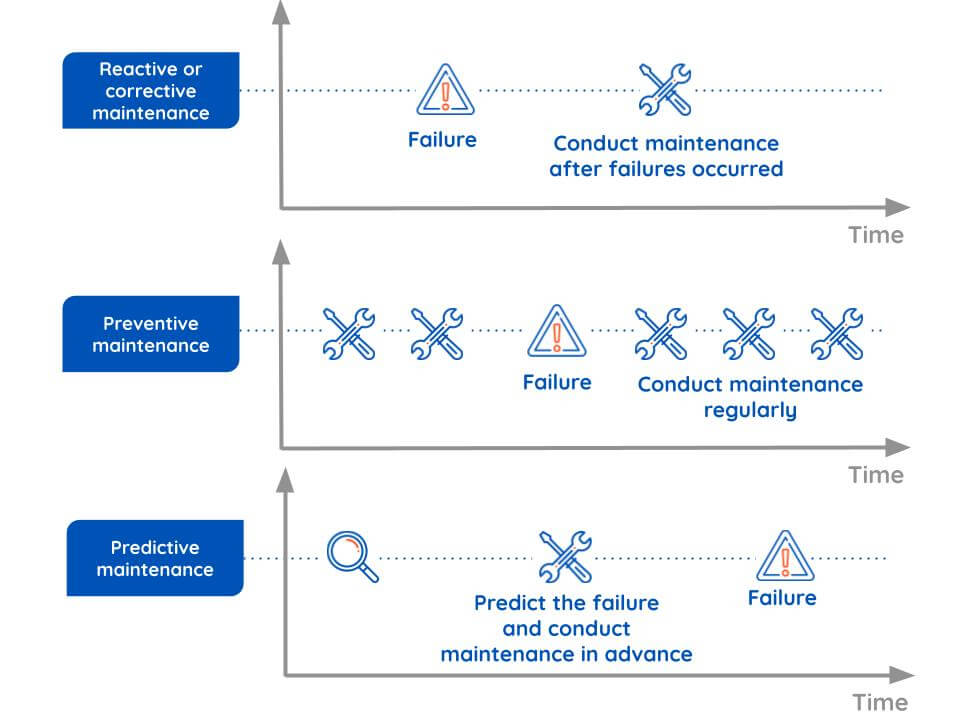
Figure 3 – Steps of principal maintenance strategies
To summarize, the maintenance function is inherent to production. Even so, understanding and quantifying maintenance activities can be problematic. The purpose of this series of scientific papers is to provide an overview of terminology, framework or models and the basic background of maintenance strategies through the use of ClickOnSite.
It considers various maintenance methods and comments on their use. Ultimately, our goal is to determine how value can be created for telecommunication infrastructures by measuring maintenance performance, examining such maintenance strategies as predictive maintenance, condition-based maintenance, etc.
Coming soon: our second chapter is dedicated to preventive maintenance.
References:
[1] European norm EN-13306 AFNOR. Maintenance Terminology. 2018.
[2] Kojchen K. and Monchy F. Maintenance: outils, méthodes et organisations efficientes.
Dunod, 2019.
[3] Ran Y., Zhou X., and Lin P. et al. A survey of predictive maintenance: Systems,
purposes, and approaches. IEEE Communication Surveys and Tutorials, 2019.
[4] R. Louhichi, Elaboration of an economic model for decision aid optimizing the
maintenance strategy of transport systems. Thèse Université de Technologie de Compiègne,
2021.
[5] Bouami D. Le grand livre de la maintenance. Afnor Éditions, 2019.
Mohamed SALLAK
Ph.D. and Associate Professor/HRD
at Heudiasyc Laboratory
in Technology University
of Compiègne (FRANCE)
More information on his background,
research fields, projects, and other publications here.