What are the facets of this maintenance? What are the best practices to adopt in the telecom industry? Here are the answers from our ITD Research partner.
©Photo: Orange Group/Christian Gesbert
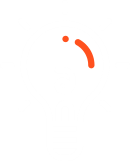
Definition
Preventive maintenance is the regular maintenance of on-site equipment to increase uptime and reduce the need for other types of maintenance (corrective and predictive maintenance). By creating a time-based schedule of inspections that occur at regular intervals (e.g. every week, every month, six months, etc.) the likelihood of equipment or a service failure can be reduced, as well as the associated losses and costs for the industrials.
The three types of preventive maintenance
There are three special forms of preventive maintenance.
Systematic preventive maintenance policy
Systematic maintenance is developed in relation to a schedule established according to the operating time or the number of usage units. Even if time is the most common unit of use, other units can be retained such as the number of items, the number of cycles carried out, etc.
It consists of systematically replacing a number of previously defined equipment even if no failure has occurred. This is scheduled maintenance. The frequency of maintenance operations is determined from commissioning and is essentially based on reliable data. This form of maintenance requires knowledge of the behavior of the equipment, the degradation modes (equipment wear), and the average or meantime of good operation between two system failures.
Conditional preventive maintenance
Conditional preventive maintenance, also known as predictive maintenance, is subordinated to a predetermined type of event (diagnostic result, sensor data, wear measurement, etc.) indicative of the operating state of the system. It depends on experience but also uses real-time data that it analyzes to determine or predict a failure.
Predictive maintenance
Predictive maintenance, also known as proactive maintenance, is also performed following an analysis of the monitored evolution of the precursor parameters of failure that qualify the operating state of the system. Proactive maintenance is a form of predictive maintenance that consists in determining the causes of failure and early wear of system equipment. Predictive maintenance makes it possible to anticipate and predict at best the moment when the maintenance operation will have to be carried out.
The metrics of the preventive maintenance
Preventive maintenance metrics are used to provide workers and managers with an accurate picture of the health and performance of all aspects of an organization. The main maintenance preventive metrics will be presented below:
- Mobilization time: normally a main part of the repair preparations. It includes the mobilization of all types of resources required. It includes all activities carried out to get the necessary resources available to execute the active repair of failed items.
- Unscheduled downtime: a metric that helps maintenance managers analyze how successfully they have implemented maintenance strategies. It is computed as follows: Unscheduled Downtime (\%) = (hours of unscheduled downtime / total period measured [inc. scheduled downtime]) * 100.
- Unscheduled downtime losses: defined to understand how downtime affects costs. it is computed as follows:
Unscheduled downtime losses (Unit per hour) = parts per hour x profit per part.
ClickOnSite preventive maintenance
For each preventive maintenance action, ClickOnSite provides a “visit report” which summarizes the service dates of all the preventive maintenance visits for the chosen site. Moreover, when specific conditions are met, a work order for an inspection is triggered.
A work order is a document that provides all the information about the maintenance tasks and outlines a process for completing these tasks. The work orders apply to a single spare part of a site or to the overall site that includes several pieces of equipment.
ClickOnSite visit report and work order composition
The visit report and the work order are composed of (cf. figure 5 and figure 6) :
- WO – ID number: the identified maintenance task
- Site ID: which indicated the location of maintenance action
- Operation & Maintenance subcontractor
- Operation & Maintenance manager
- Type of maintenance action
- The creation and due date
- The date of acknowledgment
- Work complete
- Work performed
- End of work (forecasted)
- Start of work (planned)
- Coordinates
- Work to do
- Next preventive visit in
- Next preventive maintenance visit
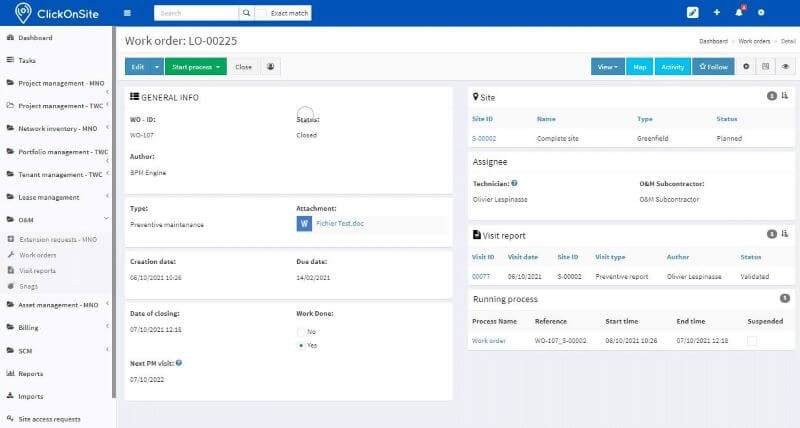
Figure 5 – Example of ClickOnSite work order
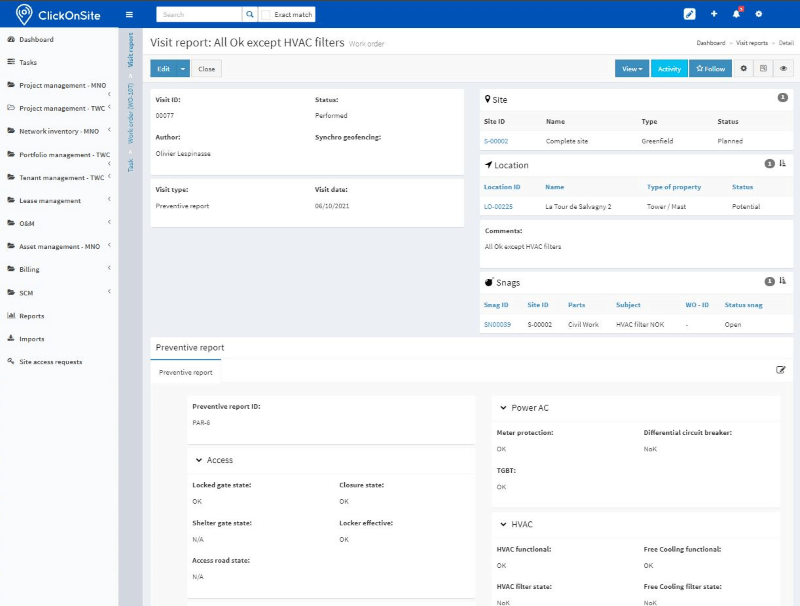
More specifically, preventive maintenance can be scheduled on a time or usage-based trigger:
- Time-based preventive maintenance: A typical example of a time-based preventive maintenance trigger is a regular inspection of a critical piece of equipment.
- Usage-based preventive maintenance: Usage-based triggers fire after a certain amount of months. An example of this trigger is a site that might be scheduled for service every six months.
In summary, how can ClickOnSite help MNOs and TowerCos?
ClickOnSite help to improve preventive maintenance by providing the following options:
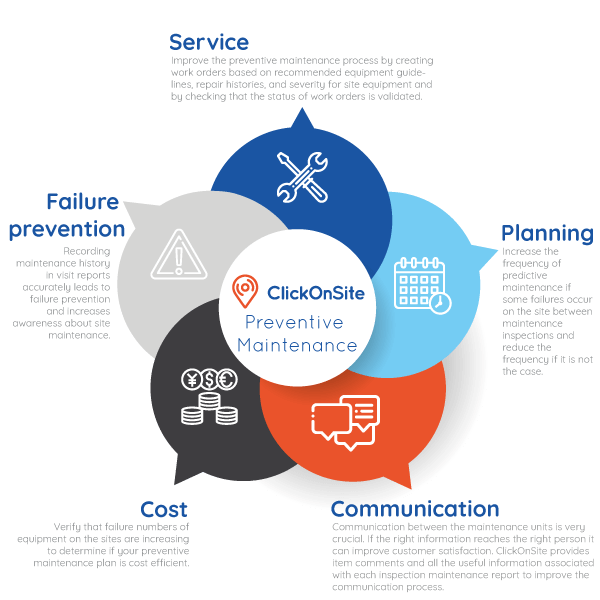
Coming soon: our third chapter is dedicated to corrective maintenance.
References:
[1] European norm EN-13306 AFNOR. Maintenance Terminology. 2018.
[2] Kojchen K. and Monchy F. Maintenance: outils, méthodes et organisations efficientes.
Dunod, 2019.
[3] Ran Y., Zhou X., and Lin P. et al. A survey of predictive maintenance: Systems,
purposes, and approaches. IEEE Communication Surveys and Tutorials, 2019.
[4] R. Louhichi, Elaboration of an economic model for decision aid optimizing the
maintenance strategy of transport systems. Thèse Université de Technologie de Compiègne,
2021.
[5] Bouami D. Le grand livre de la maintenance. Afnor Éditions, 2019.
Mohamed SALLAK
Ph.D. and Associate Professor/HRD
at Heudiasyc Laboratory
in Technology University
of Compiègne (FRANCE)
More information on his background,
research fields, projects, and other publications here.